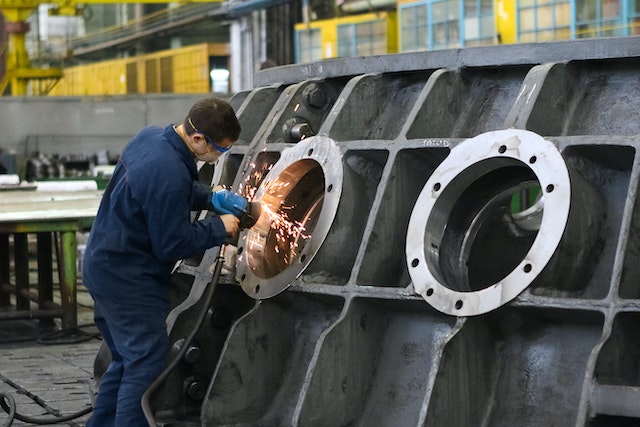
Photo by Kateryna Babaieva from Pexels
Manufacturing is both an art and science. Precision is critical in manufacturing processes, but the human element makes it challenging to achieve consistently. Mistakes can be costly, time-consuming, and even dangerous. Luckily, some common mistakes are easily avoidable with the right knowledge upfront. Research, preparation, and planning before production can help reduce the risk of pitfalls in producing your product. Let’s look at some of the most common manufacturing mistakes and how to avoid them so that your manufactured goods meet your standards and expectations from start to finish.
Choosing the wrong suppliers
If you’re not careful, the wrong supplier can quickly become a costly mistake. Take the time to select suppliers that are a good fit for your business and manufacturing process. Make sure you find out everything you can about potential suppliers before you start working with them. This includes who they work with, how they work, what equipment they have, etc. The more you know, the better informed your decision can be. You want to select suppliers that are well-known, experienced, and have an excellent reputation in the industry. Remember that you might have to work with several suppliers for different manufacturing processes, i.e., one for raw materials and a high precision cnc machining company for parts and components.
Using inadequate machinery and tools
Equipment, tools, and machinery will make or break your production process. It can also be dangerous if it is not used safely and appropriately. Before production begins, you must ensure you have all the necessary machinery and tools. It’s essential to ensure that the machinery you’re using is the correct size for your production needs. There are many variables when it comes to scaling, which could result in poor quality, wasted product, or even damage to the machinery itself. The last thing you want is to deal with a faulty machine or broken part in the middle of a production run because you didn’t take the proper steps to ensure the machinery you’re using is the right fit.
Neglecting regulations
This might not be something that immediately comes to mind. However, it’s an essential factor to consider in manufacturing. You’ll want to ensure you comply with all necessary regulations and standards. For example, you’ll want to ensure your product meets safety standards, like electrical appliances, toys, etc. You’ll also want to ensure your product meets quality standards, like for food items, other consumables, etc. If you don’t follow these regulations from the beginning, it could result in costly, time-consuming re-design or reproduction.
Failing to train staff properly
A well-trained team that understands the manufacturing process from start to finish is crucial to a successful production run. No matter what production stage your staff members are involved in, they must understand their job, the equipment they’re working with, and any potential hazards. This includes employees responsible for quality control, technicians and engineers, and everyone. Poor training can lead to product defects and costly mistakes. This is where your production planning comes into play again. You’ll want to make sure you include training in your production plan. Training schedules should reflect the project’s overall progress and be based on the knowledge and experience of your staff members.
Not carrying out regular assessments.
It’s essential to assess your production process regularly and identify potential risks or issues. You’ll want to ensure you are aware of any problems that could arise from how you produce your product. This will help you be proactive and take the necessary steps to avoid costly mistakes or issues. The best way to do this is to have regular meetings with your team members and invite other company members, including upper management, to attend. This will allow you to address issues and concerns as they arise and develop solutions. You should also consider implementing a quality control system. This system should be used throughout the production process and include a checklist that assesses critical parts of the production process.
Wrapping up
These are just a few of the most common mistakes made in manufacturing. By taking the time to identify these issues, you can better prepare yourself to avoid them.
No comments yet.